Pentair People: Herentals production team for WellMate tanks enjoy feeling the pressure.
We wrote recently about the Pentair strategic decision to establish a production line for WellMate, its flagship pressure boosting vessel, at its tank manufacturing plant in Herentals in Belgium. The relocation had many upsides for European customers. These included a considerably reduced lead time for orders, more stock availability, better alignment with European Directives for pressure equipment and ultimately a lower carbon footprint as local manufacturing considerably reduces the emissions generated by shipping containers of empty tanks across the Atlantic.
Setting up a whole new production line is no small undertaking for any manufacturer and there are multiple cost vs benefit considerations – for example, proximity to markets and materials, existing site capacity and production synergies. However, when it came to ‘labour, skills and experience’, Herentals underlined its own case. Already a Centre of Manufacturing Excellence, Herentals boasts an enviable culture of quality, precision and expertise in the team behind Europe’s largest tank plant.
WellMate production team members share their experiences
We caught up with two of the names who take great pride in the day-to day production of the Pentair WellMate ‘European’ Edition.
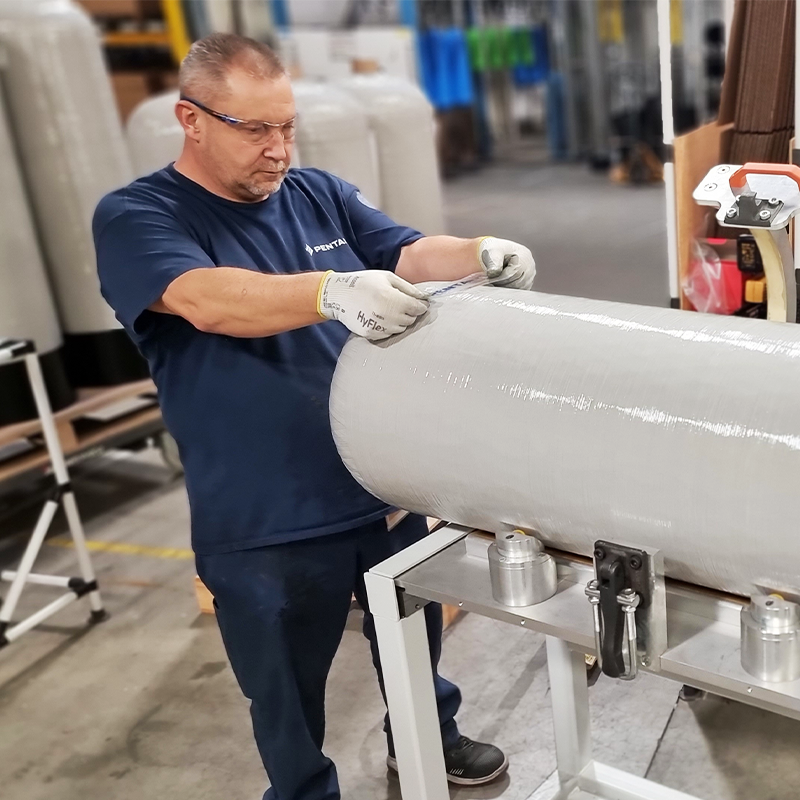
Name: Wilfried Valgaeren
Role: Assembly Specialist,
Domestic and Industrial Systems, Herentals
Experience at Pentair: 35 years
“I was delighted when I heard that Herentals had been given the opportunity to produce the WellMate Tanks for Europe. It made me feel very proud. WellMate production required special adaptation to our existing production line equipment and, as a pressurised vessel, we needed to adopt a new testing regime for them. The requirements for the European Pressure Equipment Directive (PED) are stringent. Each and every WellMate tank is tested structurally and also given an assembled ‘leak test’ using state-of-the-art helium technology, which is not only environmentally friendly but can assure 100% quality. At Pentair I have always been motivated to learn new production techniques and my journey here has been about change and improvement. WellMate production is just the latest chapter in that story.”
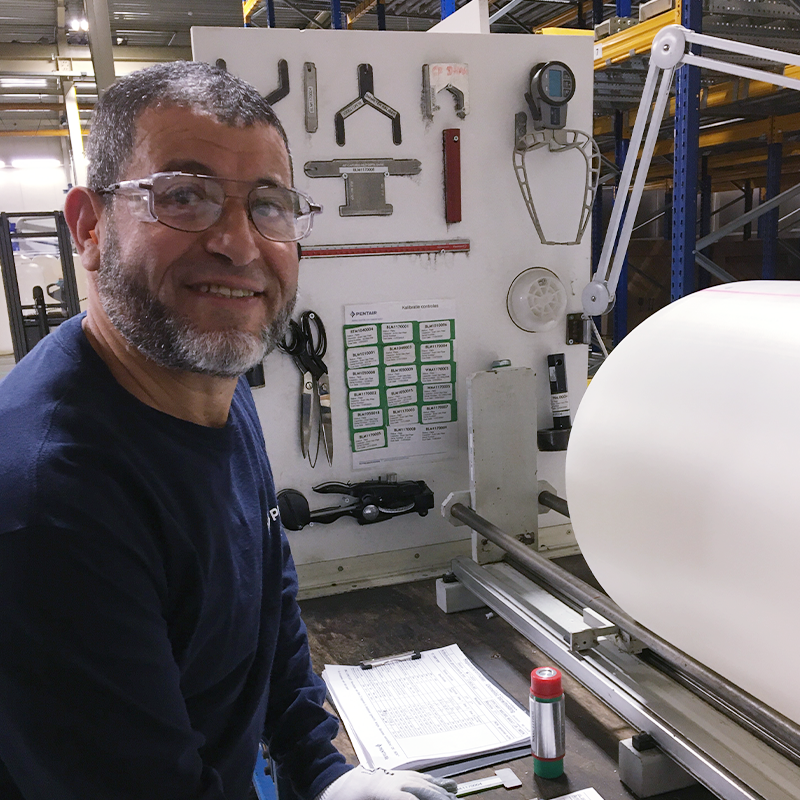
Name: Omar Hamich
Role: Specialist Blow Moulding Operator, Herentals
Experience at Pentair: 23 years
“As part of the blow moulding team, responsible for producing tank liners, WellMate represented a big change for me. Inside the tank is an HDPE, blow-moulded liner onto which we wind a stronger fiberglass layer. We then insert a flexible bladder which maintains the pressure so it is a more complex construction than most of our tanks. WellMate tank liners have two openings, one top and one bottom, which required a big change to the head of the main moulding machine. Earlier this year we literally created a hole in the roof to remove and replace the new blow moulding head! Now everything is running smoothly, my daily goal is to safeguard the quality of the liners and of course ensure that the production remains on schedule.”
‘Customer-first’ provides inspiration and motivation for a job well done
Both Wilfried and Omar are in accord on the benefits for European WellMate customers. “Unfailing quality and high customer satisfaction are hugely important to the whole team.” says Wilfried. “That counts for all Pentair products and WellMate is an opportunity to demonstrate those virtues once again.” Omar agrees, “It is a competitive market, and we always want Pentair to be the best choice for the customer’s application. It is motivational for us. With WellMate, we add another high-quality product to our production portfolio and that makes the job so much more rewarding.”
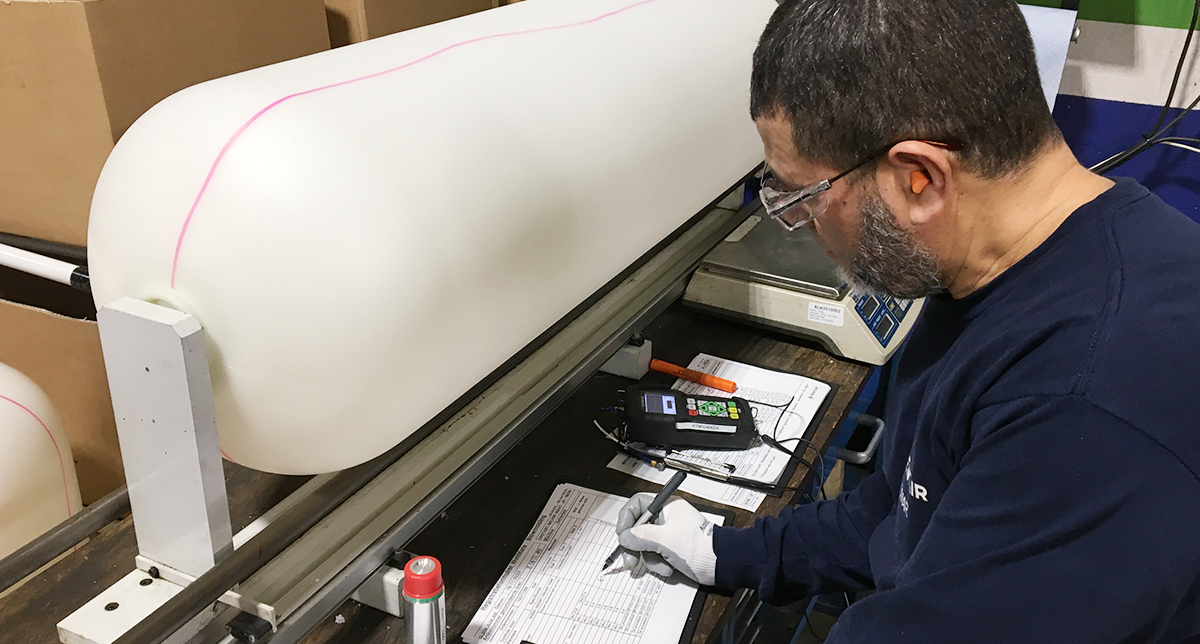