Automation transforms manufacturing processes at Pentair
The Fleck turbine meter may be a tiny component, but it has a huge story to tell.
This small yet vital sub-assembly is fitted to most Fleck residential valves and it measures the volume of water which passes through them, informing the valve controller of the optimal time for regeneration. That refresh only happens as and when it is needed, without its turbine meter a softener may unnecessarily waste a huge amount of water and salt.
But that is only part of the story. The recent history of the Fleck turbine meter is an exemplar of manufacturing best practice and beacon for the Pentair commitment to quality assurance in its European Centres of Excellence. The production team behind this tiny turbine explain how insourcing and automation are transforming Pentair manufacturing in Europe.
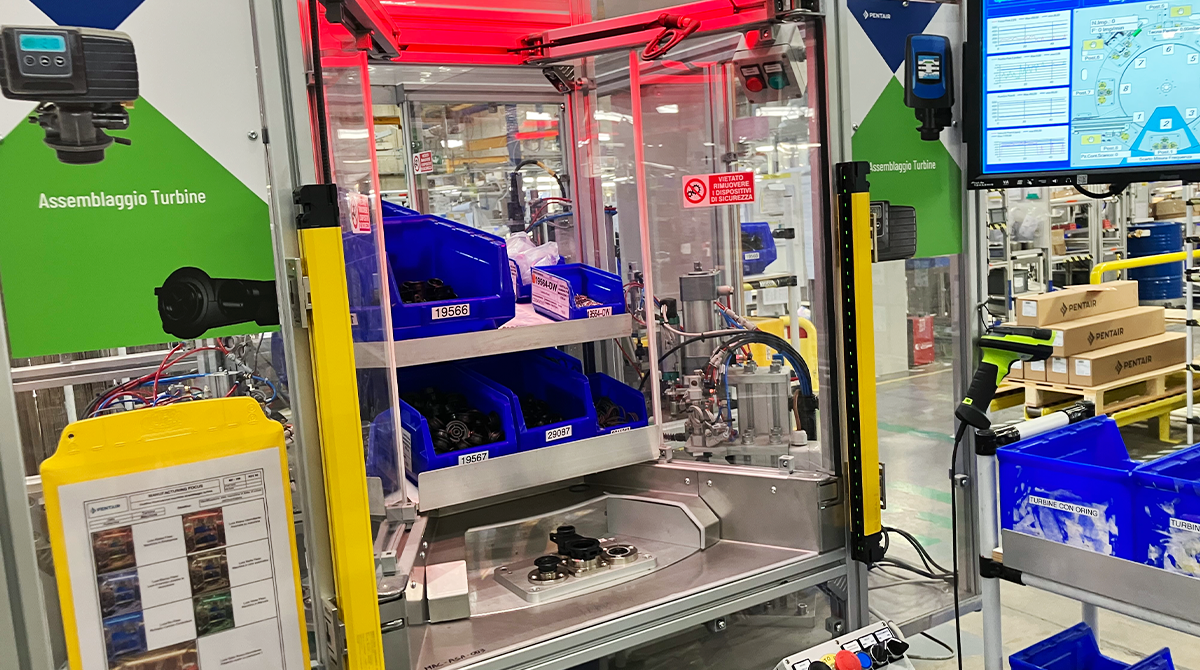
Insourcing keeps quality under control
“Three years ago, Fleck axial turbine meters were produced on our behalf by a third party,” explains Marco Calatroni, Operations Manager for Residential Water Treatment Systems at Pentair. “We enjoy a good relationship with our supply chain, but ultimately the best way to ensure quality and consistency is to do it yourself. The meter is a sensitive component and very important to the integrity of the valve. Our customers demand zero risk of failure so, in 2021, we took the decision to bring production of this component in-house.”
By insourcing sub-assembly components, like the turbine meter, Pentair has greater control over its own quality standards, better traceability and more flexibility to ramp up production according to demand. It also helps to reduce supply chain risks such as those experienced during the height of the COVID pandemic.
“When we first set up our internal production line for the turbine meter, we were essentially replicating the manual process used by our supplier. This component is quite simple, consisting of a housing, impeller and cup. But assembling to the exact tolerance is critical for the meter to function correctly. By insourcing we were able to utilise the skills of our own assemblers, to assure quality and precision, as well as control our bought-in costs.”
However, one of the key benefits of manufacturing in-house is the scope it provides for innovation and that’s exactly what happened when the production team decided to automate the assembly of the Fleck axial turbine meter.
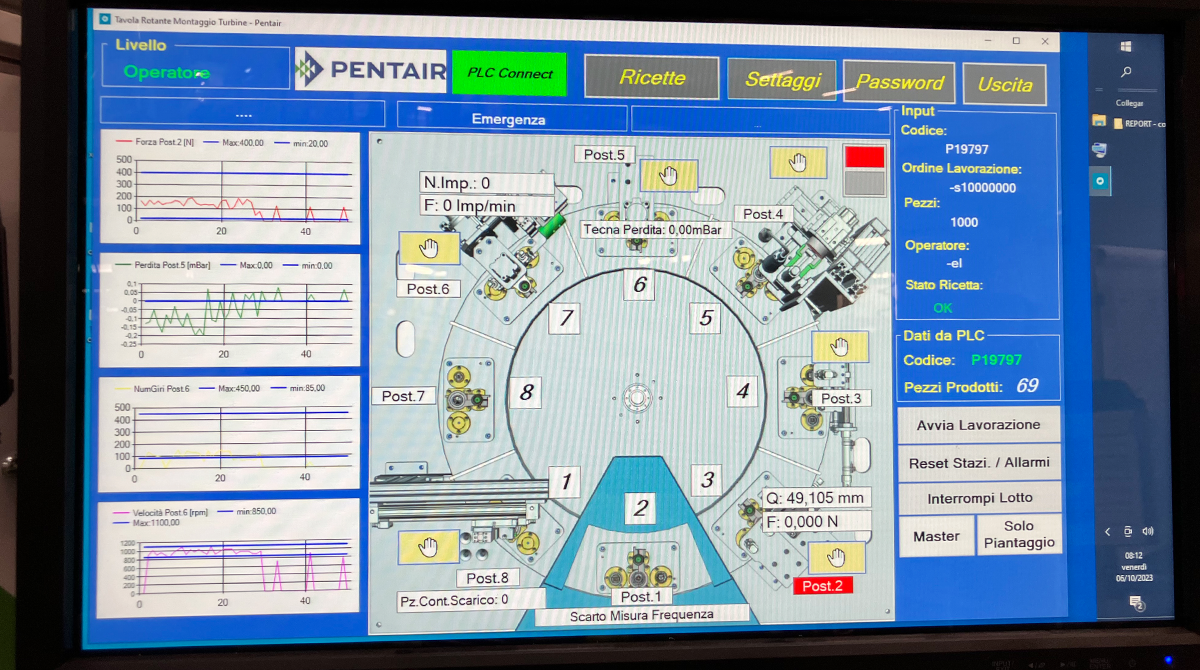
Automation brings improved precision and consistency
Leading the automation project was Pentair Manufacturing Manager, Salvatore Licitra. “Automation is revolutionising manufacturing everywhere and Pentair is no exception,” says Salvatore. “Automation can considerably speed-up the production process, improve the precision of the assembly and, as in the case of a small component like the turbine meter, reduce the risk of repetitive strain or injury to an operator.”
In 2021 Pentair commissioned a fully automated workstation for this component which came online in summer 2022 and the results speak for themselves.
“All the operator needs to do is load in the raw materials and remove the finished component from the output box. The process is 100% consistent and each meter assembly is linked to a database so we could, if needed, trace any component from any batch. The workstation also performs critical tests on every meter; an air pressure leakage test and a functional flow test. For consistency, speed, safety, traceability and efficiency this automation workstation ticks every box.”
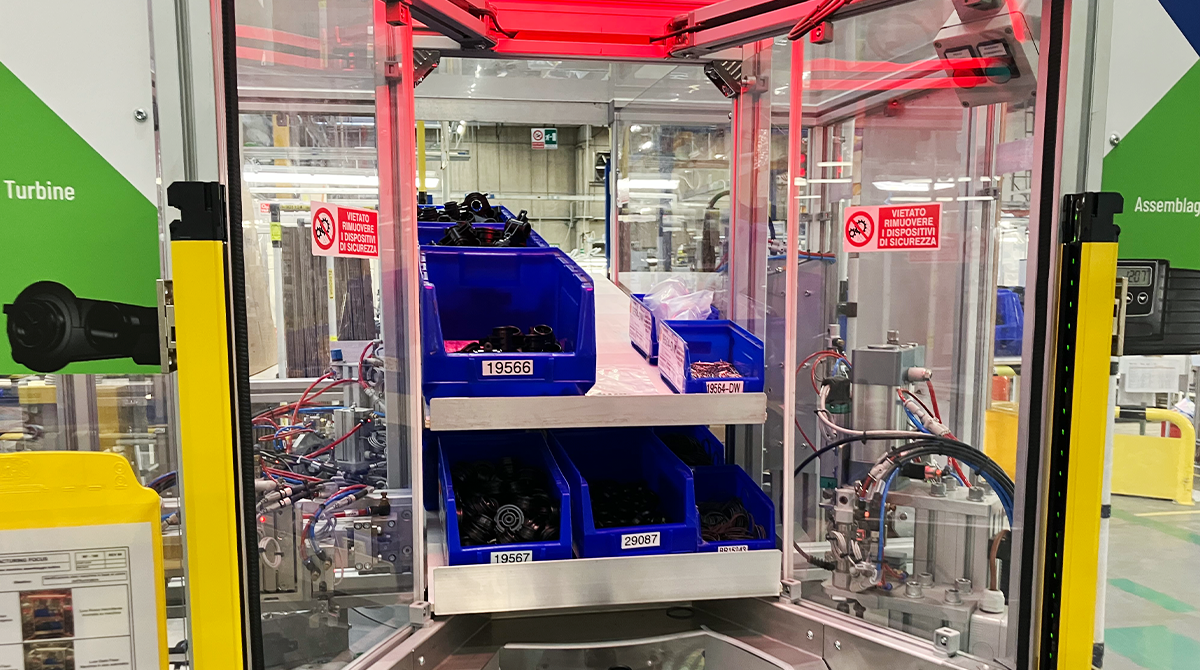
Progressive and pioneering production at Pentair
Insourcing and automation of component production, like the Fleck Axial Turbine Meter, represent a significant investment in European manufacturing for Pentair but the long-term benefits for the company, and its customers, are clear. The continued quality assurance and increased efficiency help to keep Pentair products reliable yet competitive. Automation is the future direction of travel for progressive, forward-thinking manufacturers and Pentair is increasingly adopting it in its production processes, like the Fleck turbine meter. And that is a key reason why water treatment professionals continue to insist on Pentair.