Behind every Pentair delivery is an amazing journey
Join us on a voyage of discovery to the nerve centre of Pentair distribution at Romentino, Italy.
When making a purchase, availability and supply play a crucial part in any buying decision. As consumers, we have all experienced a step-change in delivery services, where our orders arrive far quicker and more reliably than was ever possible just a few years ago.
Those expectations can only be met by advanced warehousing and logistics. As Europe’s major manufacturer of water treatment components, Pentair has invested heavily in its distribution centre at Romentino in Northern Italy. We paid a visit and met Operations Manager, Gianni Campi to discover an operation at the cutting-edge of warehouse technology.
Location is key
One could argue that the small town of Romentino in Novara, Italy has always been a ‘hub’. Its name is derived from ‘Rome near Ticino River’, so called when it was built by the Romans in the 2nd Century BC. Today Romentino boasts outstanding high-speed road and rail links in every direction and that is why Pentair chose it as a strategic distribution location ten years ago. Heading its operation day-to-day is Site Manager, Gianni Campi who explained how state-of-the-art warehouse software has transformed this part of the business.
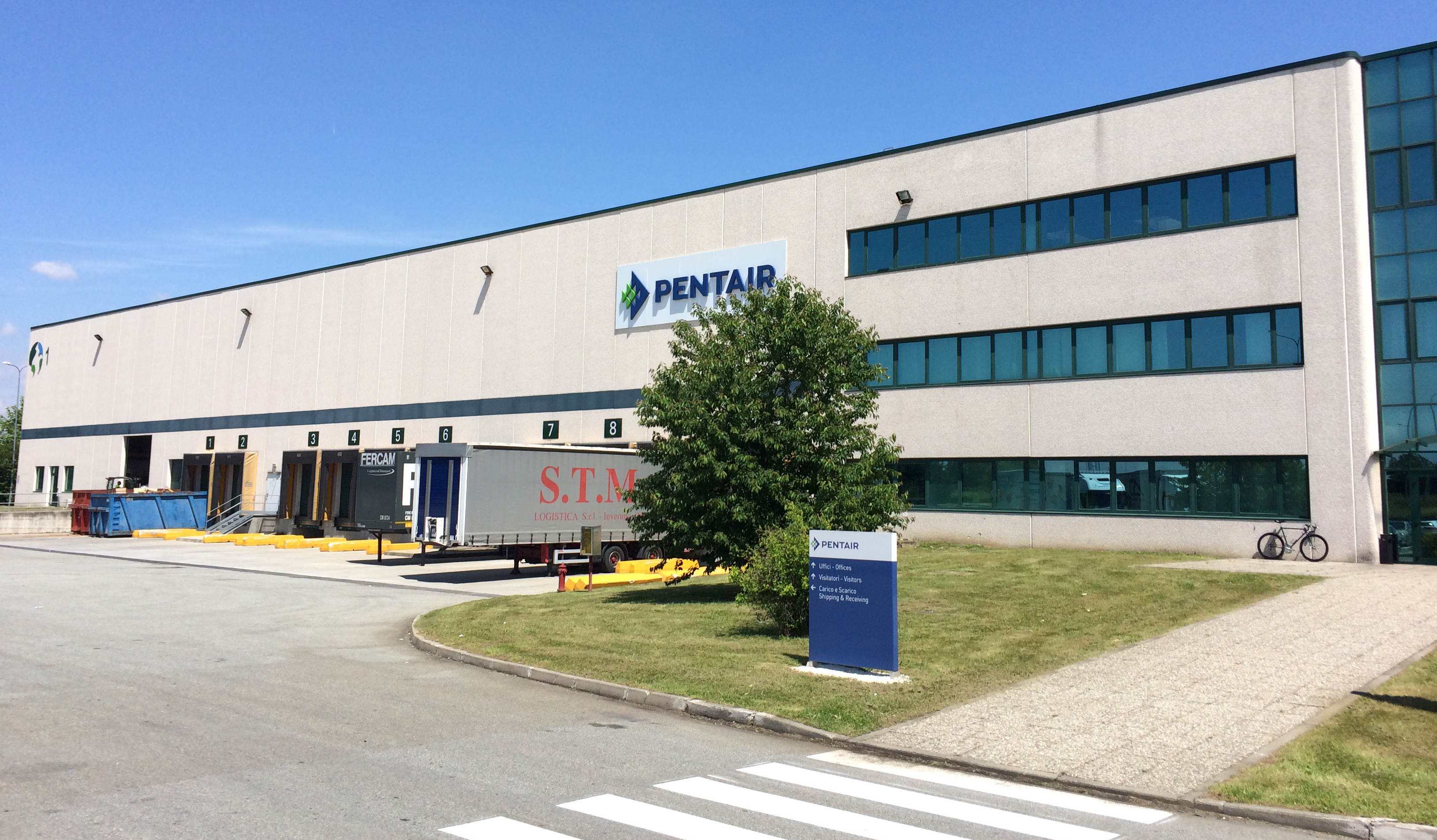
Logistics on an epic scale
“I have been working at Pentair for 22 years now, and there is never a dull day,” says Gianni. “With over 10,000 sq. meters of space, 90 employees and a 24-hour, three-shift working pattern, there is plenty going on! I think of our central European distribution facility as a ‘one-stop shop’. We receive, store and ship everything that Pentair supplies for all residential, commercial and industrial applications. From pool pumps to spray nozzles, from water softeners to ice machines, it’s a massive portfolio.”
“Although 80% of our shipments are within Europe, we actually serve 85 countries including the Americas with certain products that Pentair manufacture here in Europe. As Pentair invests more in European manufacturing at our Herentals and Pisa factories, I expect that traffic to grow.”
Inbound is a busy area with stock coming into our facility from Pentair Manufacturing Centres of Excellence in Herentals and Pisa and our sister companies across the globe. We receive about 400 container and 250 trucks a year, all of which need to be unloaded to the exact location in the warehouse. Outbound shipments go in all shapes and sizes, from a single item ordered by an installer, to a truck-load of pallets bound for a Pentair partner. Most days we see over 200 shipments leave the warehouse on route to Pentair customers.”
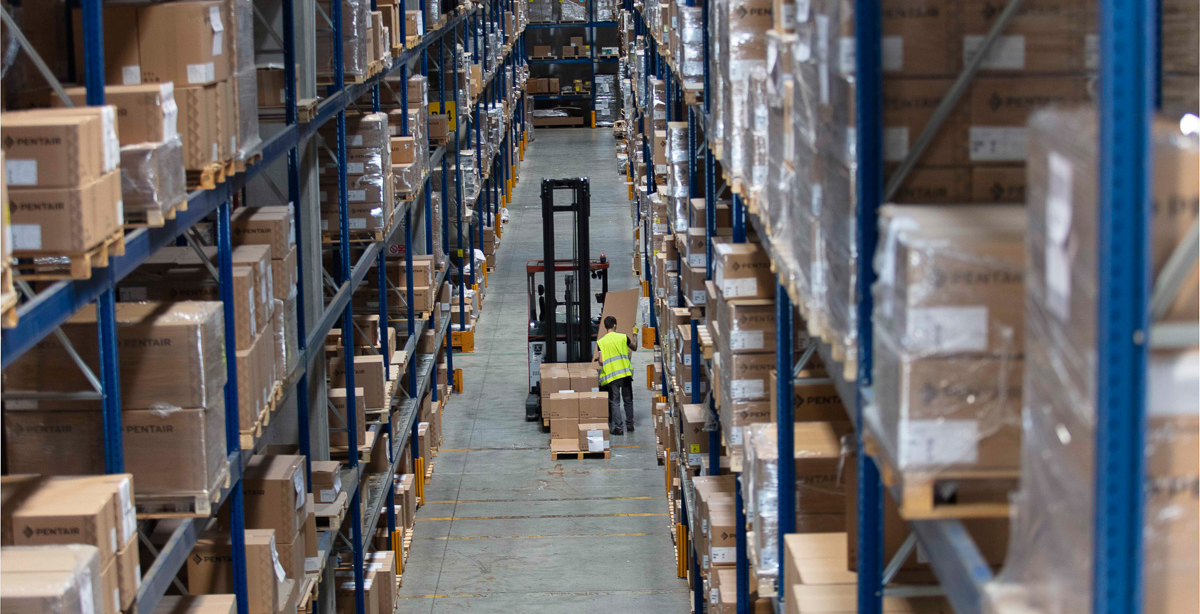
Warehouse management system drives productivity
“From day one, we wanted to ensure that our distribution facility here would make a positive impact on our customers and the business,” said Gianni. “Obviously a central European location was key. On top of that we wanted to integrate our warehouse management system (WMS) with our company-wide manufacturing systems. It has been a big investment but has led to step-change in the service we can provide.”
“One could think of the WMS as a massive database of our warehouse and every component that comes in or out of the building. Once that has been registered, the software works its magic. Like most warehouses we operate a picking and packing process. With the WMS, our pickers have a scanner that interrogates the picking list, guides them to the locations and scans everything they collect. For the packers, the scanner acts as an additional cross-check, informing them what has been picked and eliminating any mistakes on the consignment. With over 120,000 lines to choose from there would be lots of potential for errors but our WMS takes care of that. We can also measure any errors in shipments and report on how many were correct – last year it was 99.7% error free!”
Gianni is not complacent and sees the potential for improvement even in this most streamlined operation. “You can always improve one way or another and we never stop looking. We have been working with our WMS supplier to further develop our scanning and labelling processes and will introduce more enhancements in the next few months. I want to get that 99.7% up to 100% - now there’s something to aim for!”
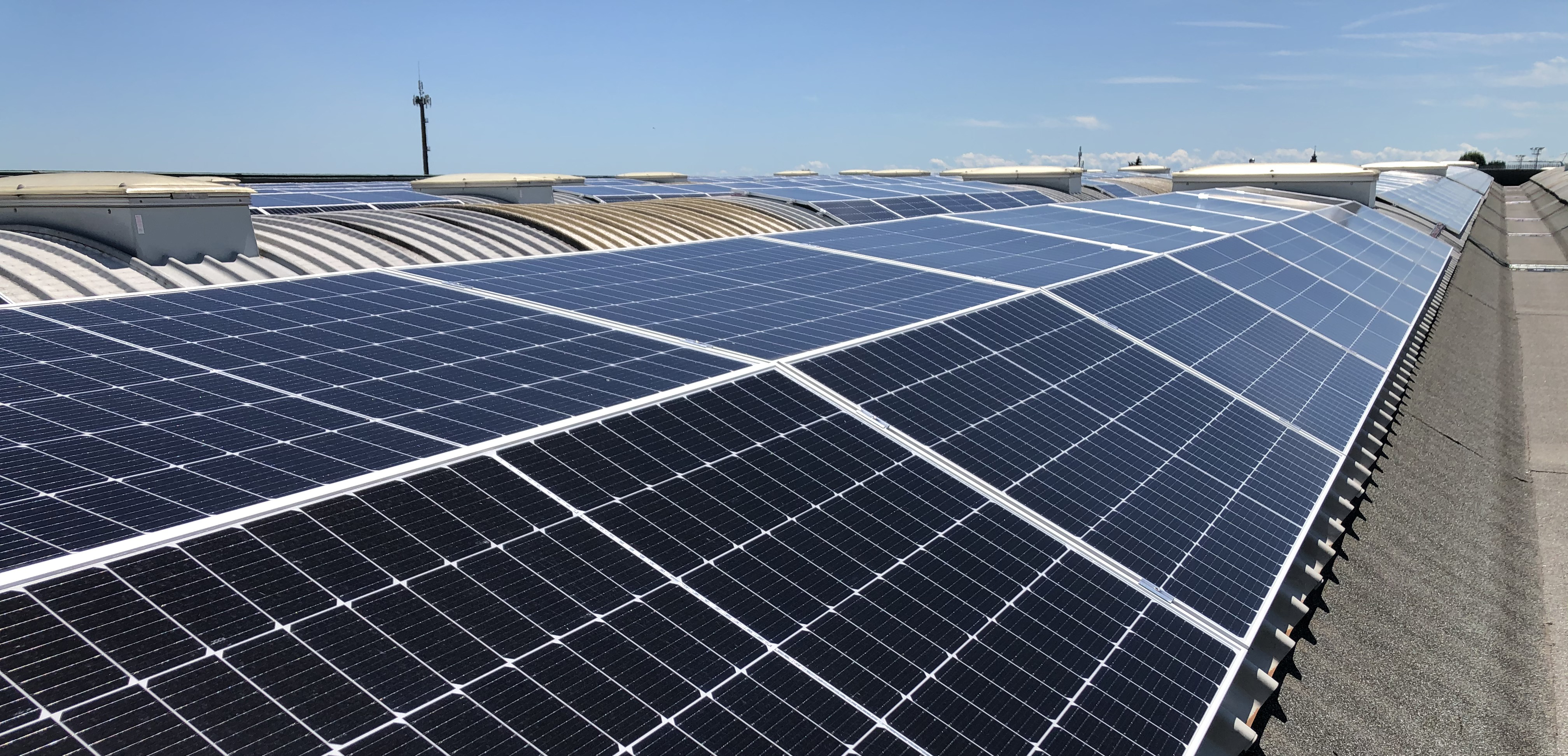
Made in Europe – delivered from Europe
Like all other Pentair facilities, Romentino is targeted to reduce its carbon footprint and has a green roadmap in place. “Everyone in the supply chain can make a difference and we are committed to do our part,” says Gianni. “We insist our freight-forwarders only use trucks that are certified and fully compliant with the European emission standard Euro VI. We have driven down our own emissions by installing all LED, sensor-controlled lighting in 2018, and thanks to the installation of solar roof panels last year we are energy self-sufficient too.”
Understandably our customers don’t see what goes on behind the scenes, they simply get the right goods at the right time. But there is a fantastic journey behind every component, from its manufacture in a Pentair European Centre of Excellence via our state-of-the-art distribution centre to its final destination.
Our team and software ensure the orders are streamlined, we can be accurate about our delivery dates and the feedback from customers is glowing. It is one of the many benefits of choosing to order from a company who manufacture and distribute in Europe for Europe.